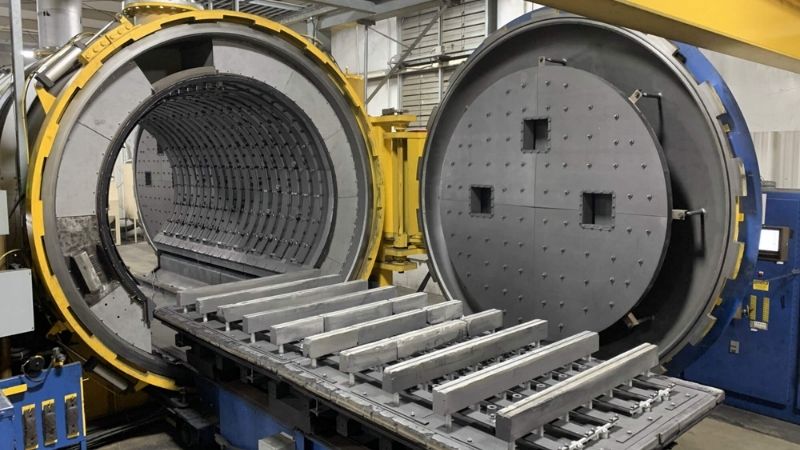
Understanding Heat Treatment Fixtures
In the heat treatment process, fixtures play a vital role. These structures hold or support parts during heating, cooling, and quenching operations to ensure uniform treatment. Traditionally, heat treatment fixtures were made from metals like steel, titanium, or nickel-based alloys due to their ability to withstand high temperatures.
However, these materials come with inherent drawbacks:
- High Weight: Metal fixtures are heavy, leading to increased energy consumption for moving and heating.
- Thermal Expansion: Metals expand when heated, sometimes causing distortions that can affect part quality.
- Limited Durability: Prolonged exposure to high temperatures can cause metal fixtures to wear out or deform over time, necessitating frequent replacements.
To address these challenges, the industry has turned to Carbon Fiber Composite (CFC) fixtures, which are proving to be a superior alternative.
What Are CFC Fixtures?
CFC fixtures are made from carbon fiber composite materials, which combine lightweight carbon fibers with a resin matrix. These composites are designed to operate in extreme temperature environments, making them ideal for heat treatment applications.
Key characteristics of CFC fixtures include:
- High thermal resistance: Capable of withstanding temperatures up to 2000°C.
- Low thermal expansion: CFC materials exhibit minimal expansion, preserving the shape and alignment of parts during heat treatment.
- Lightweight: Carbon fiber is significantly lighter than traditional metals, making it easier to handle and reducing energy consumption.
Benefits of CFC Fixtures in Heat Treatment
The adoption of CFC fixtures is revolutionizing the heat treatment process in several ways:
1. Energy Efficiency
One of the most compelling benefits of CFC fixtures is their lightweight nature. Traditional metal fixtures, particularly those made from steel or alloys, are heavy and require more energy to heat. In contrast, CFC fixtures are approximately 5-10 times lighter than their metal counterparts. This drastic reduction in weight leads to significant energy savings during the heating process, as less mass needs to be heated.
By consuming less energy, companies can reduce operational costs, lower their carbon footprint, and contribute to more sustainable manufacturing processes.
2. Improved Part Quality
Maintaining the integrity of the parts during heat treatment is critical. Metal fixtures often expand under heat, causing the fixtures to distort or shift the parts being treated. This thermal expansion can lead to inconsistencies in the final product.
CFC fixtures have a low coefficient of thermal expansion, meaning they maintain their shape even at high temperatures. As a result, parts are held more securely in place, leading to greater uniformity in the heat treatment process and improving the overall quality of the treated components.
3. Longer Fixture Lifespan
Another key advantage of CFC fixtures is their durability. Traditional metal fixtures are prone to wear and tear from repeated exposure to high temperatures. Over time, metal fixtures oxidize, corrode, and lose their structural integrity, leading to frequent replacements.
CFC fixtures, on the other hand, are oxidation-resistant and exhibit superior thermal stability. They do not degrade as quickly as metal fixtures, resulting in a longer operational lifespan. This reduces downtime for fixture maintenance and replacement, allowing for continuous production and lower overall fixture costs.
4. Reduced Maintenance and Downtime
The durability of CFC fixtures not only extends their lifespan but also minimizes maintenance requirements. Metal fixtures require frequent inspections and upkeep due to wear and oxidation. In contrast, CFC fixtures are resistant to corrosion and degradation, resulting in lower maintenance needs and fewer operational disruptions. This contributes to increased productivity and higher throughput in heat treatment operations.
5. Enhanced Design Flexibility
CFC fixtures can be designed and engineered to meet specific requirements, offering greater flexibility than traditional metal fixtures. Carbon fiber composites can be easily shaped into custom forms to accommodate various part geometries, leading to better support and improved heat treatment outcomes. This flexibility also enables the design of more efficient and compact fixtures, reducing material waste and further enhancing energy efficiency.
Applications in the Industry
CFC fixtures are being widely adopted in industries where precision, durability, and high-performance materials are critical. Some of the sectors leading the charge include:
- Aerospace: High-strength, lightweight components are crucial in the aerospace industry, and CFC fixtures ensure parts maintain their integrity during heat treatment processes.
- Automotive: With the rise of electric vehicles and the demand for lighter, more efficient parts, the automotive industry is increasingly utilizing CFC fixtures for treating complex components.
- Medical Devices: The need for precise and reliable heat treatment in medical device manufacturing has driven the adoption of CFC fixtures for producing high-quality instruments and implants.
Conclusion
The heat treatment industry is embracing Carbon Fiber Composite fixtures as a revolutionary technology that enhances efficiency reduces costs, and improves product quality. With their lightweight nature, superior thermal stability, and long-lasting durability, CFC fixtures are quickly becoming the go-to solution for businesses seeking to optimize their heat treatment processes. As industries continue to evolve and demand more energy-efficient and sustainable practices, CFC fixtures are poised to play an increasingly prominent role in the future of manufacturing.
By investing in CFC fixtures, companies can achieve higher productivity, better quality control, and long-term cost savings—a true revolution in the world of heat treatment.